Manufacturing of Refrigerators
OVERVIEW
What you need to know
VA-SCS specialises in the sale and lease of both new and used refrigerated containers (reefers) and portable units for cold storage and transportation purposes.VA-SCS supply all types of top quality refrigerated containers to the domestic and international markets. VA-SCS is a market leading specialist in the sale and lease of both new and used refrigerated containers and temperature controlled units.
As action expanded, VA-SCS extended and made an upkeep and 24H crisis fix administration. The spotlight was especially on taking a stab at quality and a superb help that kept our clients returning to us.
This series of case studies seeks to understand better the role of services in global value chains (GVCs) and examine how policies may impact the configuration, location and operation of value chains. The company in this case study is a Japan-based multi-product conglomerate that specializes in infrastructure systems, energy solutions, and information and telecommunication systems. It also produces a range of capital goods, consumer goods, and services, including logistics, distribution, and financial services. This case study explores a value chain that manufactures, sells, and services home appliances.
Total revenue of the group was over USD 4 billion in FY2013. Home appliances account for approximately 10 per cent of the group’s revenue. Key products for the consumer market include refrigerators, air conditioners, vacuum cleaners, rice cookers and other home appliances.
The company has a global production and distribution network. In addition to manufacturing plants in Japan, within the Asian region the company has established important manufacturing bases in Thailand, Malaysia, the Philippines and China. Each of the facilities is responsible for the production of one or more product categories for its domestic market and for exports. The company’s biggest market is its home market, where products are sold in the company’s own 4,500 sales outlets as well as through other retailers. The company also owns a number of subsidiaries in South East Asia, India, Middle East, the United States and the United Kingdom for sales, marketing and after-sales services.
This case study focuses specifically on the manufacture of refrigerators in Thailand. The company’s Thai factory is located in an industrial estate in the neighborhood of Bangkok, and it produces a wide range of products in the company’s portfolio. The factory has approximately 5000 staff, with 30 Japanese engineers. Refrigerators are manufactured in this factory and shipped to markets in Southeast Asia and East Asia. Issues arising in respect of the value chains of other products manufactured at other production sites will also be discussed to provide a comprehensive view of policy affecting the home appliance sector.
Related services
- Designing
- Project management
- Strategic sourcing
- Owner’s inspections
- Quality leadership performance
- Manufacturing consulting
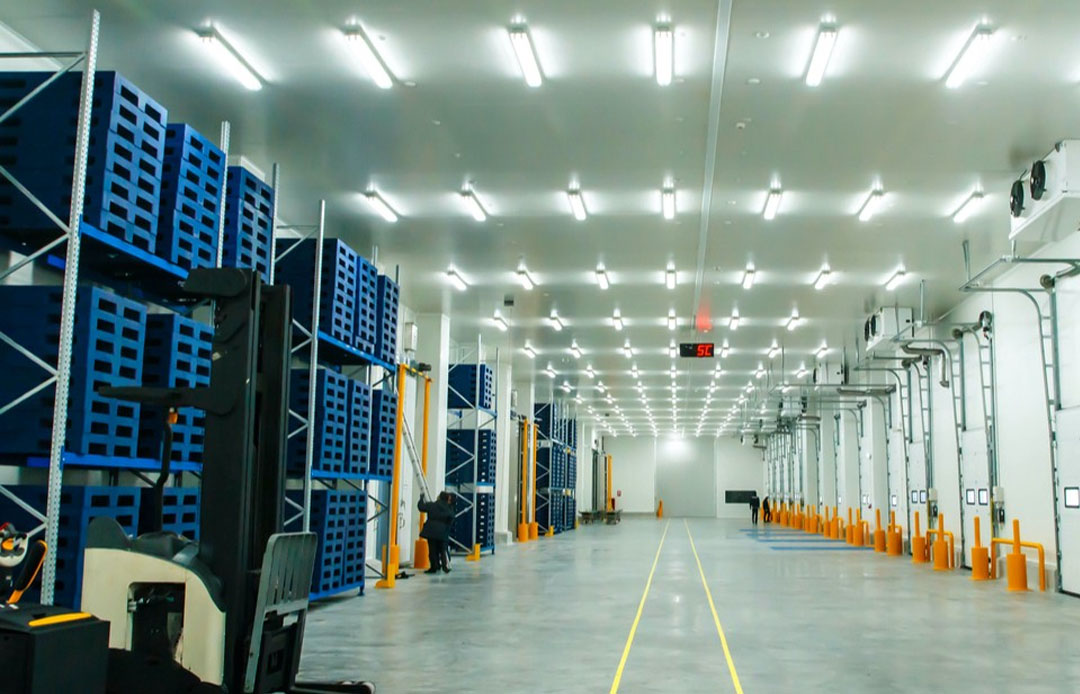
FEATURED
Why Choose Us?
Industries Transportation & Distribution is committed to helping its clients reach their goals, to personalising their event experiences, to providing an innovative environment, and to making a difference.The case study is structured in the following way. Part 2 will map out the value chain. Part 3 will analyze how services enter the value chain. Part 4 will discuss how policies relating to foreign investment restrictions, foreign labor restrictions and other areas affect the value chain.
Mapping the Value Chain
The company, together with its affiliated companies, is involved in every stage of the value chain from pre-production procurement of raw materials and parts to after-sales customer services. The value chain begins at the procurement of raw materials and parts. Modern refrigerators require a long list of inputs. The exterior shell is usually made with metal and coated with paint. The interior cabin is usually made from plastics. Metal sheets, chemicals for the paint, and plastics are procured locally from third party suppliers. Key components such as compressors and motors involving technologically advanced manufacturing are procured within the firm’s family of companies. To guarantee quality, most of them are manufactured in either factories of the group in Thailand or imported from the group’s factories in Japan
Modern refrigerators such as the company’s product involve the use of computer chips and programming software which are also provided from within the company group. All the materials and components are shipped from suppliers to the manufacturing plant by an affiliated logistics company. This logistics company supports the group’s international operations by providing international forwarding, warehousing and distribution services. The Thai subsidiary of this logistics company is an affiliate in which the group owns minority shares. Raw materials and components are shipped to the factory by sea, road or rail.
After the raw materials arrive in the factory, they are stored in on-site warehouses before they are used on the manufacturing line. A typical refrigerator manufacturing process requires the assembly of three parts, namely the exterior shell, the interior cabin and the cooling mechanism. Standard procedures for manufacturing the outer shell involve cutting and welding sheets of metal into appropriate sizes and spraying them with a coat of paint. The interiors of the refrigerators are usually made of plastic that require moulding and shaping before being placed on the assembly line. Tubes for refrigerant, water and electrical wires must be installed within the inner cabinet and connected to the mechanical parts. The back panel is then assembled with the compressor and storage tank for refrigerant. Finally, the doors are installed and fitted with seals. The assembly line will put together all these components.2 After the refrigerators pass their post-production quality inspections, they will be packed with foam and boxes and shipped to distributors in Thailand, as well as overseas markets.
The company has subsidiaries in many economies who act as distributors. The company does not own retail outlets in Thailand, but they work with local retail stores and distribution channels that eventually become their long-term business partners. The company works with these partners on marketing, sales and post-sales services. The company prepares advertising materials and plans advertisement campaigns for its products. In addition, the company hires agents to promote the company’s products in retail stores. Home electrical appliances of the company come with warranty services for repair and maintenance for up to five years. Many of the repair service stations are outsourced to retailers, while some are maintained in-house by the company. Complicated maintenance operations requiring specialized engineering services will be brought back to the company. The company maintains call centers for technical supports to customers. In addition to typical after-sales services, the company also provides recycling services in Japan. Business customers who purchase the company’s products may also negotiate hire purchase plans supported by the financial services arm of the group. To support a global value chain, a comprehensive set of back-office services is required. Among them are various management services, utilities and research and development for new products which help the company to maintain its cutting edge. Service companies owned by the group contribute to product designs by collecting feedback from customers and user experiences.