Our Services
OVERVIEW
Industries Served
Our industries are experiencing basic challenges. From climate change and geopolitics to the energy market, we are facing new reality. Some people consider them a threat. At Industreis, we believe our job is to turn them into opportunities.
That's why we look for new ways to use our expertise in the energy industry, discover new opportunities and promote innovation around the world. Our ambition is to become the world's most efficient industrial solutions and services provider.
Our featured
Support 24/7
Maintenance support
A full services
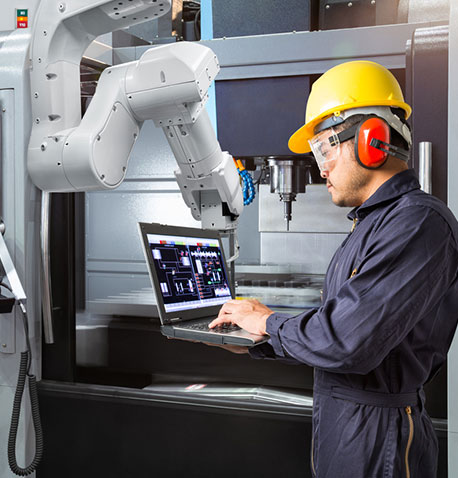
OUR SERVICES
What we do
Switch gear Manufacturing
a wide range of reliable and dependable switchgear products which are widely recognized by all clients and consultants...
View detailsPower distribution Panels
With the aim to meet the varied Power Distribution Panel requirements of our customers....
View detailsTransformer Source Panels
World-class epoxy resin cast dry-type transformer design and manufacturing processes introduced from Portugal and Germany,...
View detailsRefrigerators
VA-SCS specialises in the sale and lease of both new and used refrigerated containers ...
View detailsFabrications
With IoT business solutions, manufacturers have the power not only to improve and automate production,...
View details3rd party inspection Test plan
Third Party Quality Inspection that refers to the quality part of work. In this part an inspection agency...
View detailsServices in the Value Chain, Outsourcing and Bundling
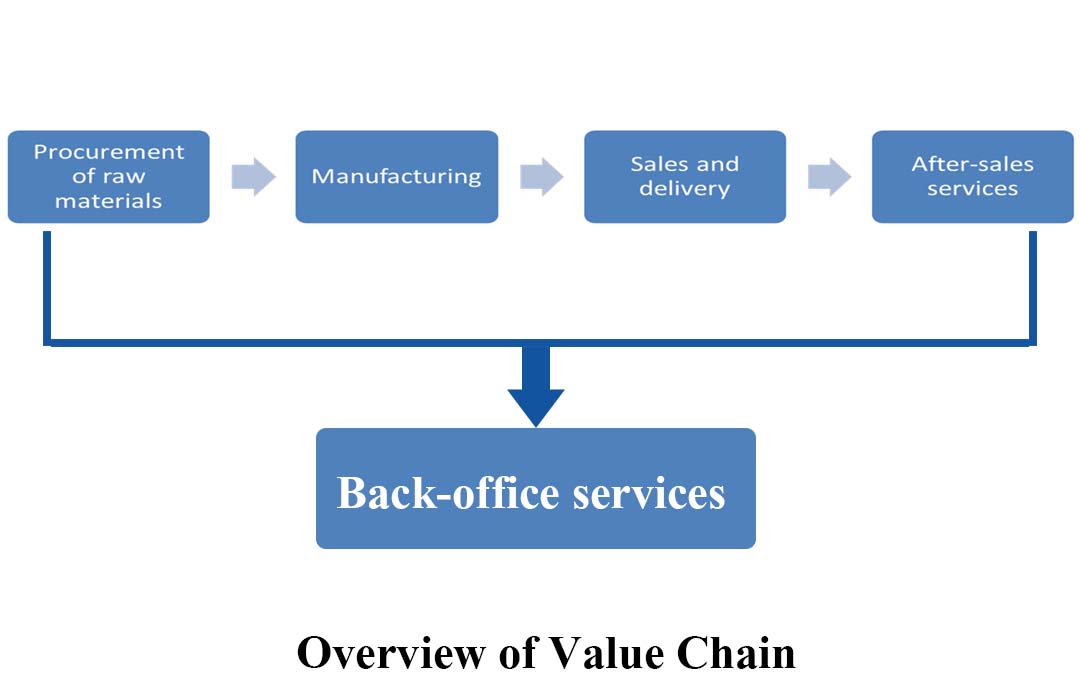
Value Chain
For ease of analysis, the value chain is disaggregated into five stages, namely pre-manufacturing,manufacturing, sales, back-office services, and after-sales services. A list of services inputs to the value chain can be found in Appendix A.
The number of services that are used in this value chain is estimated to be 55. Approximately half (25) of the services are back-office services, followed by 12 in the manufacturing stage, and 9 in the procurement process for raw-materials procurement. The large number of service inputs at the backoffice stage is not surprising for a complicated GVC that requires support services at every stage of the chain.
Outsourcing
Among the 55 services in the value chain, 31 services (56% of all services) are outsourced or partially outsourced to third-party services providers who are not members or affiliates of the group. There are three main reasons why the company outsources service inputs in the value chain. The most common reason for outsourcing is for efficiency and cost saving. With modularization of tasks in GVCs, third parties can compete to be part of the value chain of multinational corporations (MNCs), offering quality services at lower costs. The company, as the lead firm in the value chain, can outsource services for cost minimization. In some industries, outsourced suppliers may be able to attain economies of scale therefore they are capable of providing services to the company at a lower cost than the company would be able to provide itself. An example is the MNC that provides IT services to the company. The IT service provider is able to take advantage of its existing network, allowing it to operate IT functions at a lower cost than if the company operated the functions itself.
Lack of expertise, local knowledge or local connections are other reasons for outsourcing. Local connections in some economies are essential for the company to expand to the market more efficiently. That is one of the reasons why the company cooperates with local retailers with long-term business relationships rather than operating in-house retail stores.
Government regimes may sometimes necessitate outsourcing. When these services are efficiently supplied, they add value to the company and to society as a whole. For example, safety inspections in factories help to minimize the likelihood of industrial accidents; standard conformity requirements ensure products are safe for public use, also adding to the goodwill enjoyed by the company. On the other hand, if government lacks the capability to carry out policy efficiently, deadweight social and private costs may be incurred.
Bundling
Bundling is a way of offering goods together with services in a single offering. This can enhance efficiency, support innovation, and help the company generate higher revenues from their products. In this value chain, the company offers warranties for their products. This is essentially bundling insurance, and repair and maintenance services with the physical product. The company expands its product portfolio in this way. It also creates a positive signaling device to customers on the quality of the products, enabling company to sell more products and at a price premium. The same happens on the input side when the company purchases machinery that is bundled with maintenance.
VA SCS Owner’s Inspection Service
Value Added supply chain solution bring trust and ethical standards to Global Trade in line with the Voice of customer. Our top priority is to avoid costly product defects and shipment delay, Identify the corrective actions, Protect Customer’s brand from poor quality. VA will take responsible to Conduct and monitor the supplier quality performance throw DPU, DPH & PPM based on VOC.
Rigorous Strategic Sourcing
- Our Sourcing solution methodology aims to rapidly demonstrate savings to the bottom line whilst being highly analytical to make objective supplier selection decisions.
- Factory visitation and qualification review to guarantee reliable, ethical vendors across entire supply chain.
- Our business model is to work exclusively for the benefit of the buyer with no preferred relationship with any of the suppliers. In this way we are totally focused towards achieving our client’s objectives and continuously improving their procurement performance.